And the “Oops” Business Award goes to…
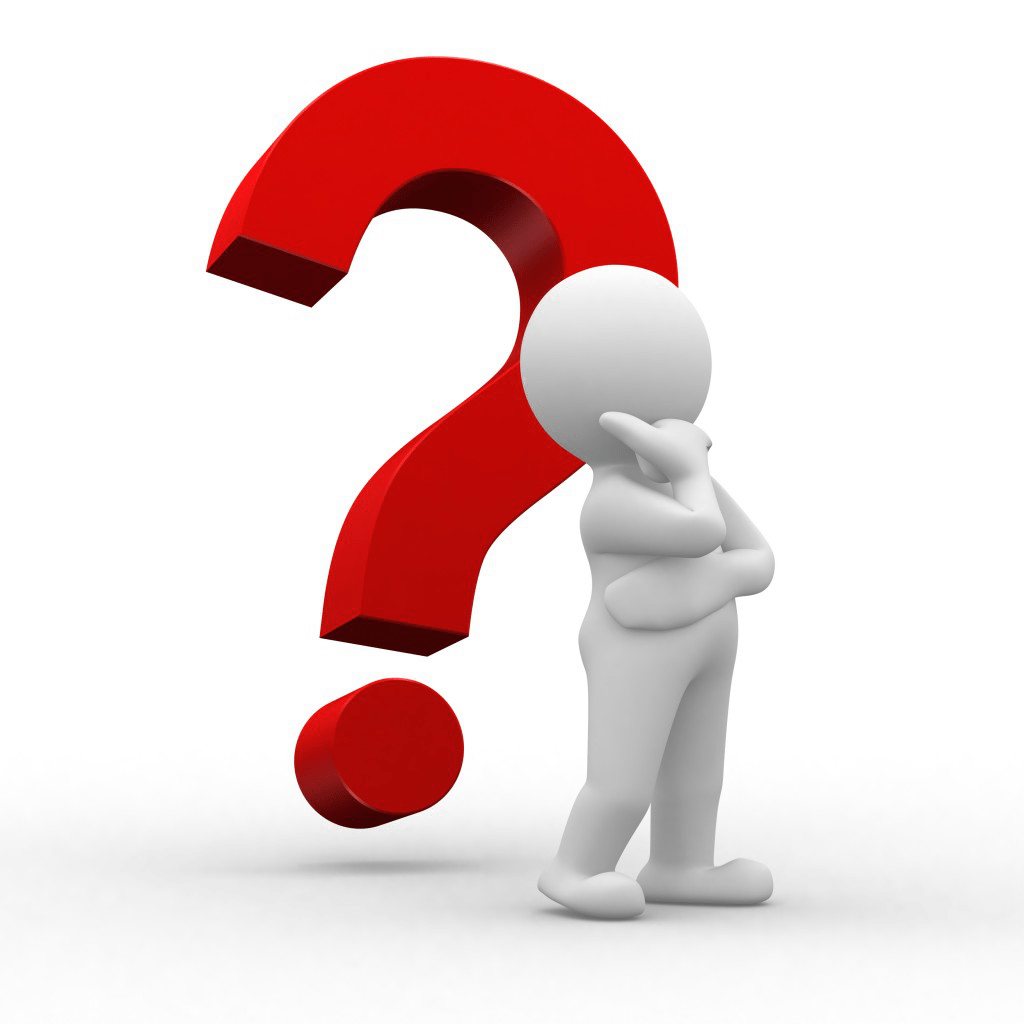
If you are in the Awards business, at some point, you will say, “Oops we made a mistake”. Once said, you have a limited amount of time to rectify the problem. In addition, “how” you decide to move forward can be more important than the mistake itself.
Recently, we had to say “Oops” to an Award customer. My company designs and manufactures custom business Signage and Awards. We had a relatively new customer who placed a reorder of an item. The Award and the layout remained identical, however, the business name changed.
Although we have a Quality Policy, and orders are sent through several checks and rechecks, mistakes happen. We also send a proof to the customer. Once the customer has signed off on the proof, the item is put into production.
Orders are processed through customer service, and the approved file is sent to production. As an extra check, we opened each award box and cleaned each item to be sure the names were correct. We labeled each box for easy identification for the customer. The awards were delivered.
The customer distributed the items to company personnel. This is when the mistake was noticed – the last line of type on the award was missing.
Four sets of eyes, yes four sets of eyes, missed the mistake. The Customer Service Representative, the Customer, the Engraver and the Salesperson.
Once the mistake was communicated to all parties, and after we all got up off the floor, we went into “fix” mode. First was to assure the customer we would correct the problem at no cost to them. Even though the customer “signed off” on the proof, it was our mistake, and we needed to take responsibility. If we tried to play hardball, we would have lost a good customer. We picked up the awards from the customer.
So what happened? First we determined that when the awards were typeset, each line was separate. At some point, when a long name was entered, the last line of type was knocked off. That was easily corrected by changing the file set up into one group – if there’s an overage, the entire design will be moved.
Next, we decided to also proof internally before production. Although we ask the Customer to proof the items, ultimately, its our responsibility to make a the customer satisfied. Finally, we sent the awards back through the engraver to add the missed line of type. We delivered the order and the customer was happy.
Ultimately, no one minds an occasional “oops”. The key is to ACKNOWLEDGE AND CORRECT QUICKLY!
Please visit
WWW.EXCELSIORMARKING.COM and
WWW.EXCELSIORSIGN.COM
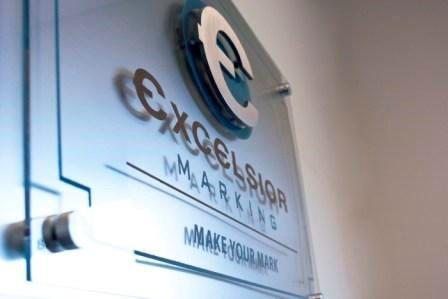
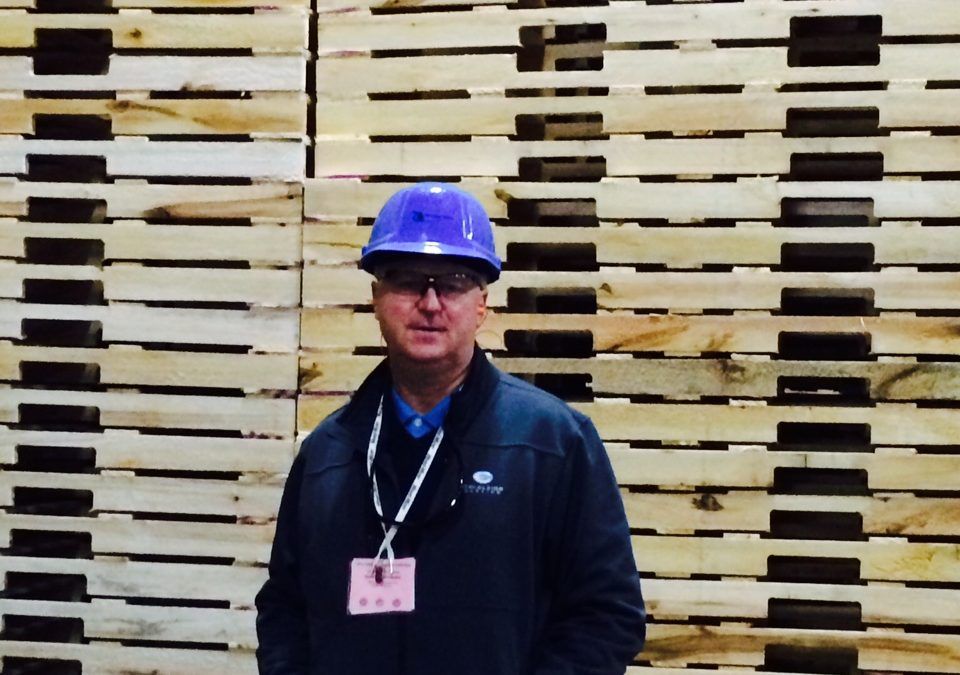
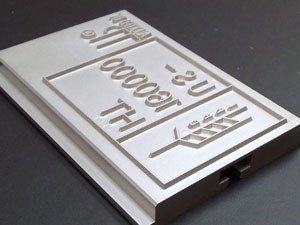
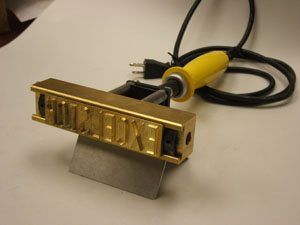
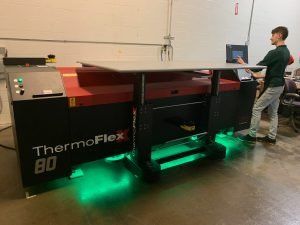

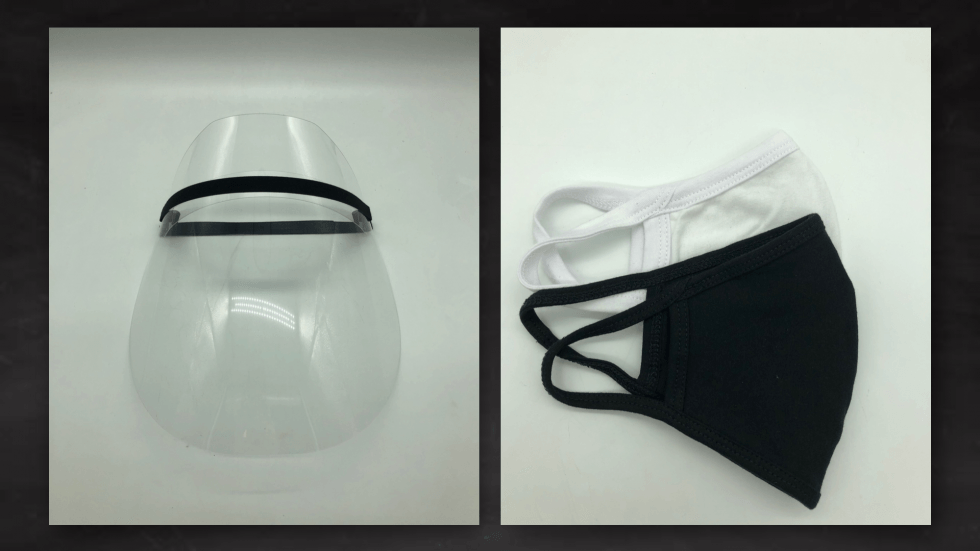
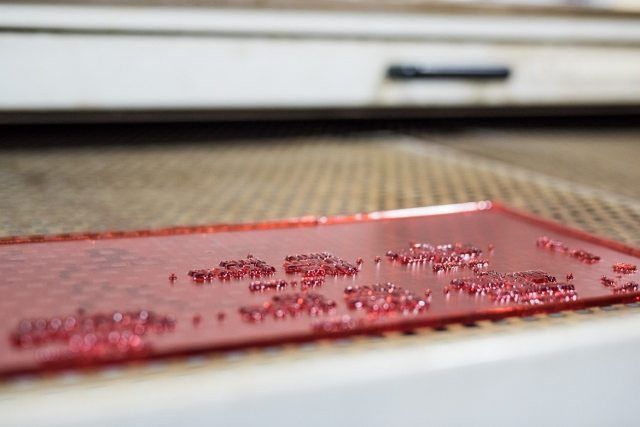
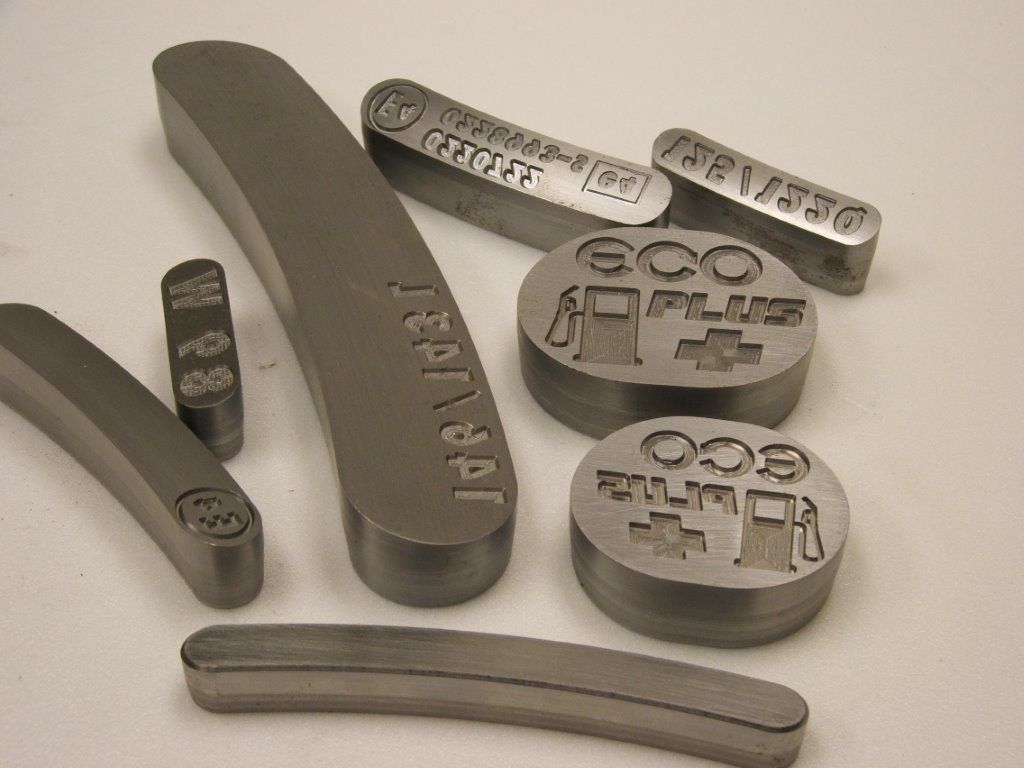
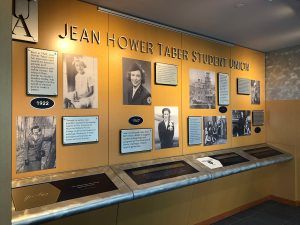
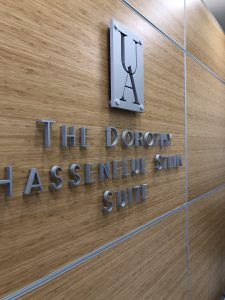